| Manual transfer stations: Australia Post specifies Rotacaster The Problem Australia Post used ball transfer tables for manual sorting of bulky international mailbags weighing up to 35 kg. This required substantial and repetitive manual effort by operators to push, pull and rotate the bags, exposing them to potential musculoskeletal injury. | 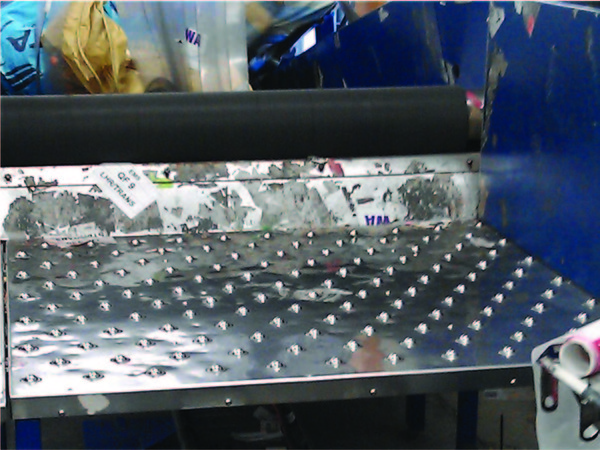
| | The Challenge: To address this issue Australia Post looked for alternative solutions that would substantially reduce operator input and exposure to risk of injury. With a targeted push/pull force of 50N (5kg) for a 35Kg bag, it was acknowledged that this target would in all likelihood require a powered solution, adding to operating and maintenance costs.The problem: Australia Post used ball transfer tables for manual sorting of bulky international mailbags weighing up to 35 kg. This required substantial and repetitive manual effort by operators to push, pull and rotate the bags, exposing them to potential musculoskeletal injury. | | Rotacaster Solution: Rotacaster proposed a manual transfer solution utilizing their 48mm Rotacasters combined with polyacetal (POM) spacer rollers. The roller’s smaller diameter was designed to provide support for the soft packaging, while minimizing friction and reducing the number of Rotacaster wheels required. Australia Post and Rotacaster collaborated on the design and construction of the transfer table. Trials were successfully undertaken at an Australia Post gateway. | | 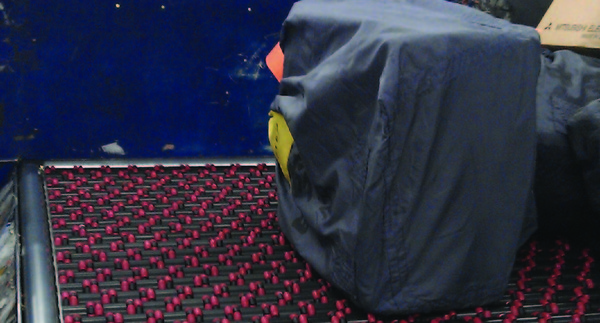
| |
Outcome: The solution resulted in a significant reduction of push/pull forces to between 40 and 70N (4-7kg) in all directions on the table. Australia Post considered this a remarkable achievement in the absence of any powered assist.
Additional Advantages: In addition to reducing the push/pull forces required, without the cost noise and maintenance associated with a powered solution, the polymer surfaces of the Rotacasters and spacer rollers have demonstrated a lower affinity to adhesion of labels and stickers from packages, further reducing down time and maintenance costs. | | Comment: Rotacaster CEO Peter McKinnon notes “Feedback from operators using the table has been exceptionally positive. And importantly, the risk of injury has been reduced. Rotacasters are proving their versatility.” Implementation: With this extremely successful trial result, the remaining transfer tables at this Gateway facility will be replaced with the Rotacaster solution, with further upgrades to follow in Sydney, Brisbane and elsewhere. | |
Type: Transfer Table, air mail Load: 35Kg (77lbs) User: Australia Post Country: Australia
|
| | Narrow Milk Crate RotatruckThe Challenge:
A leading Australian manufacturer and distributor of beverages and milk products needed to improve its milk distribution and reduce manual handling risks. Replacing its current hand-trucks, the solution needed to suit not only their specific distribution centre needs, it also needed to integrate into the supply chain. | 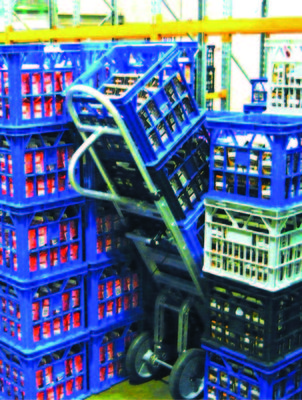 | The Rotacaster Solution:
Rotacaster developed a specialised Rotatruck to not only pick-up the milk-crate stacks from the floor and delivery pallets, but to be able to retrieve crates from between crate stacks. To complicate matters, the client needed to be able to handle two different crate styles. To meet the client’s needs, Rotacaster developed a new narrow-isle wheelbase and adapted Rotacaster ’s patent-pending adaptable latching system, designed to securely autoengage the milk-crates, to work inside the narrow body as well as adjust to different crate heights. A second solution was developed to pick-up two crate stacks at a time to further improve productivity, especially when interfacing with the supply chain, specifically the loading and loading of large trailers. The solutions reduce the effort required to transfer crate stacks, improves safety and productivity, especially critical to the supply chain, specifically. The Milk-Crate Rotatruck has adopted widely across a range of organisations including dairies. We estimate that in 2014 more than half of Australia’s packaged milk will be transferred on Rotatrucks. The solution requires no power and minimal maintenance, while delivering reliable and improved productivity. |
|
| | Milk-Crate Rotatruck for Woolworth Australia The Challenge:
Leading Australian grocery retailer Woolworths needed to improve its back of store operations resupplying milk into the rear-loading display fridges. The objective was to reduce injuries, increase productivity and improve the user experience. | | The Rotacaster Solution:
Rotacaster developed a specialised Rotatruck to pick-up the milk-crate stacks from the delivery pallets and deliver them to the fridges, from where individual bottles could be transferred into the display. The solution significantly reduced the amount of bending required as well as the effort required to transfer the milk from the crates to the display. In addition to a 12 month multi-site trial, movement specialist dorsaVi electronically analysed flexion and forces with and without the Rotacaster solution and found significantly reduction in both, as well as improved productivity. This data was confirmed in the final data generated by the trial across a substantial number of sites.
The milk-crate Rotatruck is fitted with Rotacaster ’s patent-pending adaptable latching system, designed to securely auto-engage the milk-crates. Woolworths has decided to roll-out the Rotacaster solution across most
of its stores. While considered a significant capital investment, ROI is expected in 90 days. Since then the Milk-Crate Rotatruck has been adopted more widely across a range of organisations including several dairies. We estimate that in 2014 more than half of Australia’s packaged milk will be transferred on Rotatrucks. |
|
| | Bread Crate RotatruckThe Challenge:
A large commercial baker was looking for an ergonomically safe way to move stacks of 12 and 15 bread crates. These stacks are 1.80m and 2.25mm tall respectively. Fully loaded they weigh as much as 185Kg with a challenging very high centre of gravity. Traditional hand trucks required the operator to support the load, making it difficult to see past the load when moving forward. | 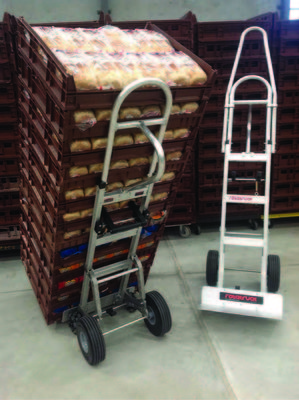 | The Rotacaster Solution:
By adopting the self-supporting Rotatruck, the company was able to focus it’s staff on safely guiding the crate stacks while transferring them, rather than having to primarily support them. This significantly improved the ergonomic handling qualities for the user, including reduced fatigue. To secure the crates to the truck, Rotacaster developed a patented self-engaging latching system that is easily disengaged after placing the crate stack. Productivity is further improved by the use of the multi-directional Rotacasters fitted to the front of the wheelbase and enabling precise multi-directional manoeuvrability.
Importantly, the use of Rotacasters allows the easy change of direction without destabilising the tall load, as unlike traditional swivel casters, Rotacasters are in a fixed mount. The solution requires no power to the wheels and minimal maintenance, while delivering reliable productivity.
|
|
| | Hand Truck for Liquide NitrogenThe Challenge: Air Liquide Health Care Australia needed a compact solution that would transport two liquid nitrogen dewars
and two medical oxygen cylinders with minimal load tilt. Solution:
Rotacaster developed a specific two wheel hand truck to meet these requirements and the strict rules associated with handling liquid nitrogen.
It consists of a light but robust folding aluminium frame and an extra large folding toe to accommodate the two liquid nitrogen dewars and provide a compact solution.
An additional frame mounted rubber extrusion significantly reduces the risk of damage to the dewars while attached straps stabilise and secure the load.
A sturdy bag fixed between the frame enables the transportation of up to two additional oxygen bottles. Other features include a release strap that enables the toe to be folded without bending, and the reduced handle height allows the operator to minimise the load tilt. 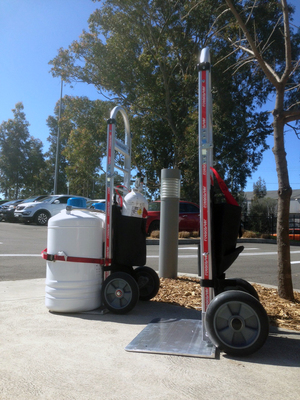
|
|
View Page | 1234 | Next > |