| White-Goods Hand Truck The Challenge:
A large Mexican white goods distributor needed to improve the handling of the large and tall loads such as washers and dryers. Using traditional 2-wheel hand trucks, the user had to negotiate their way without being able to see well as they had to balance the heavy load which put considerable ergonomic stress on the body. | | The Rotacaster Solution:
By adopting the self-supporting Rotatruck, the company was able to focus it’s staff on safely guiding the load down the aisles, rather than having to primarily support them. The self supporting feature enables the user to
walk offset from the load and see where they are going. This significantly improved the ergonomic handling qualities for the user, including reduced fatigue. Importantly, the use of Rotacasters allows the easy change of direction without destabilising the tall load, as unlike traditional swivel casters, Rotacasters are in a fixed mount. |
|
| | BWS Self-Supporting Rotatruck The Challenge: Leading beer, wine and spirits retailer BWS needed to improve the handling of the heavy loads involved in moving cartons of it’s product. Using traditional 2-wheel hand trucks, the user had to negotiate their way through narrow isles while balancing the heavy load which put considerable ergonomic stress on the body. Likewise, the manual loading and unloading of the trolly required a lot of bending and flexing.
Type: Self Supporting Rotatruck™ Capacity: 100Kg (220lbs) User: BWS Country: Australia Reseller: Rotacaster Fabricator: Rotacaster The Rotacaster Solution: By adopting the self-supporting Rotatruck, the company was able to focus it’s staff on safely guiding the load down the isles, rather than having to primarily support them. This significantly improved the ergonomic handling qualities for the user, including reduced fatigue.
Loading and unloading was also improved by the 2 phase self-supporting position. Fewer pull-backs also considerably reduced strain on the operator. Importantly, the use of Rotacasters allows the easy change of direction without destabilizing the tall load, as unlike traditional swivel casters, Rotacasters are in a fixed mount. The solution requires no power to the wheels and minimal maintenance, while delivering reliable productivity.
Another winning Rotacaster solution.
|
| | Pallet Repair StationThe Challenge:
An Australian pallet manufacturer company was in need of a robust multi-directional transfer solution for its pallet inspection, maintenance and repair station. This is a hard and dirty business, with 250,000 pallets annually passing through and being inspected, cleaned and repaired on the transfer table. | | The Rotacaster Solution:
To objectively compare, they installed three solutions across three lines: ball-transfers, steel omni-wheels and 125mm Rotacasters. Three years and 750,000 pallets later only one is left standing. First to go were the ball-transfers. Every week required either maintenance or replacement as they were fast to wear under the heavy
impact of the pallets and repair work. Next to fail were the steel omni-wheels. Environmental and physical impact eventually started getting the better of these wheels. Last standing and fully operational remained the
125mm Rotacasters, which after three hard years showed virtually no wear and tear, required no maintenance, and delivered day in - day out. | 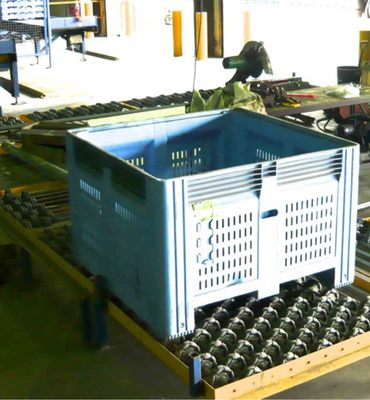 | The result:
All maintenance stations were converted to use Rotacasters.
The solution requires no power and minimal maintenance, while delivering reliable and improved productivity. |
|
| | DC Inline Transfer Table The Challenge:
A large US consumer goods manufacturer was looking to improve workplace ergonomics and productivity in its distribution centre. They needed to be able to manually rotate received boxes and move them to load onto a pallet. The boxes are gravity-fed to a workstation with a conventional conveyor roller bed. At this workstation, operators are required to sort, orientate and offload boxes onto a pallet for shipping. The forces required to orientate and slide the boxes on conventional steel rollers were a target for improvement, especially considering the repetitive nature of the operation | | The Rotacaster Solution:
Rotacaster US reseller Magnus Mobility proposed a manual transfer solution utilising their 48mm Rotacasters. Arranged as shown inside the standard conveyor frame and not needing any significant modifications the Rotacasters were spaced to optimally support the load and allow for easy rotation and movement. | | The Outcome:
After trials on the initial line, the manufacturer has moved to expand the solution across as 12 stations. Further expansion is planned for the future. The solution resulted in a significant reduction of push/pull forces originally required to rotate and transfer the boxes. After the successful trial on one workstation, the distribution centre
is now planning to upgrade all workstations. The solution requires no power to the Rotacasters and minimal maintenance, while delivering reliable productivity. |
|
| | Precision Fitting TableThe Challenge:
American Ceramic Technology Inc. (ACT) needed to inc rease productivity and improve workplace ergonomics in the fitting of grommets to their Silflex™ radiation shielding. The original workstation it was ergonomically challenging, requiring a two handed effort to position the up to 200lbs heavy Silflex™ blankets to precisely
install the grommets. | The Rotacaster Solution:
After investigating several options for an improved workstation, including an air table, ACT opted for the Rotacaster multi-directional wheel. Working with Integrator Prime Resource Inc, ACT developed a workstation
using 48mm Rotacasters framed in modular T-slot aluminum extrusion from 80/20 Inc. The wheels were sourced from Rotacaster reseller Magnus Mobility Systems. The chosen wheel density provides excellent load support, very easy movement and the ability to precisely positioning of these relatively heavy blankets. The SilflexTM radiation shielding blankets are now manoeuvered and positioned easily with one hand eliminating the need to lean, twist and pull the item into place.
The new workstation exceeded all expectations for increased productivity and improved ergonomics while saving ACT over 75% in acquisition costs compared to the installation of an air-table. The solution requires no power to the Rotacasters and minimal maintenance, while delivering reliable productivity and improved
safety. | 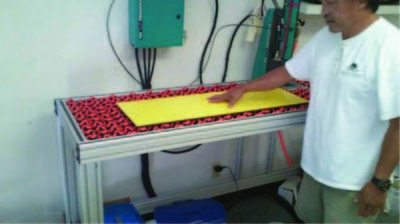 | |
|
|
View Page < Previous | 1234 | Next > |